The productivity of employees may be affected when risks at work increase and are not properly managed. Safety hazards may exist at any corner of the workplace, be it at the back-end office, the maintenance room, the production section, the cleaning facilities, the warehouse, the construction site, and more. Hence, it is everyone’s duty especially the employer or safety managers to monitor, measure and identify potential accidents to prepare necessary protection to ensure the health and well-being of the employees at work.
No workplace is the same and so, the safety hazards are different in each industry. Early assessment minimizes the level of injuries, accidents, downtimes, or asset damages.
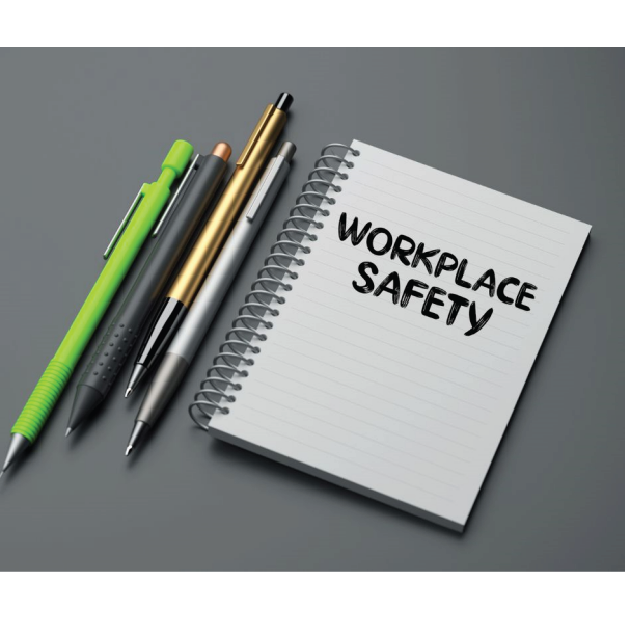
1. Spills & Trips
These hazards happen in circumstances with cluttered walkways, blocked aisles, slippery surfaces, poor lighting, and more. Accident rates can be minimized by keeping walkways clear, adding signages or marking on wet floors, and improving lighting in the workplace.
2. Fall from Height
Working in an environment that involves performing tasks at an elevated condition for example above the ground or floor level and carries the risk of like falling from one level to another means working at height. Based on Malaysia’s regulations, working at a distance above 10 feet is considered high risk and proper personal protective equipment (PPE) should be equipped to minimize injuries or accident rates.
Safety guidelines and procedures when working at height must be carried out to minimize the risk of accidents. Appropriate equipment like safety harnesses, safety lines, guardrails and lanyards, proper ladders, scaffolds, or other equipment designed for working at height are some of the common gears to prepare for employees.
3. Electrical Hazard
Exposed wires, faulty electrical equipment, overloaded circuits, improper grounding, and misuse of electrical equipment are prone to electrical shock and electrocution risks. Electrical insulating protective equipment like rubber-insulating gloves and boots and insulating mats are commonly used to minimize electrical shock. The protection should be extended with regular electrical safety inspections, electrical safety training, and proper maintenance of electrical equipment. In addition, employees should be encouraged to report any electrical hazards they observe and should be trained to follow safe electrical practices in the workplace. PPE that is damaged or worn out should be replaced immediately to ensure adequate protection.
4) Chemical Hazard
Chemical hazards can result from exposure to toxic substances, including chemicals such as solvents, acids, and gases used in the workplace which can cause serious injury, illness, or even death. Employees involved in different kinds of exposure need different types of personal protective equipment.
For instance, using a respirator to reduce inhalation of toxic fumes or vapours and usage of protective clothing and skin protection, such as gloves, aprons, and face shields if prone to skin contact with the chemical. Apart from the appropriate protective equipment, proper chemical storage places, training on the safe handling and disposal of chemicals as well as proper emergency response procedures in the event of a chemical spill or release are required to minimize these hazards.
5) Biological hazards
Personal protective equipment (PPE) plays an important role in biological safety in the workplace. Biological hazards can include exposure to bacteria, viruses, and other microorganisms. Provision of personal protective equipment, proper hygiene practices, and maintenance for a clean and sanitary workplace is the common practice to minimize biological hazards.
PPE that is commonly seen and used during the outbreak of Covid-19 includes protective coveralls, gloves, and face shields/goggles to protect against splashes of contaminated fluids and respirators/face masks to protect against inhalation of airborne particles and droplets. Any PPE that is damaged or worn should be replaced immediately to ensure that it provides adequate protection to employees.
6) Fire Hazard
Fire hazards are a serious safety concern in the workplace and can cause property damage, injury, and death. It usually occurs due to improper storage of flammable materials, overloaded electrical circuits, and improper use of equipment. To minimize fire hazards, fire safety programs that include fire drills with proper evacuation procedures, fire safety training, and fire safety inspections should be implemented regularly. Fire alarms, blankets, and fire extinguishers need to be placed at locations likely to catch fire and employees should be encouraged to report any fire hazards they observe.
7) Noise Hazard
Loud machinery and equipment tend to cause noise hazards which links to hearing pollution. Employers can minimize these hazards by providing hearing protection like ear plugs or muffs, maintaining equipment to minimize noise, and implementing soundproofing measures.